Northeastern's Transformative Robotics Lab

Capstan Clutch
Spring 2024
Scope: 8 months
Role: Research Assistant
Problem: Design, manufacture, and test a market viable Electrostatic Capstan Clutch with a 100 Nm holding torque using optimized values
Final design CAD
Overall Size: 58 mm Diameter, 140mm length
Previous tests have been conducted on the theory of a Capstan Clutch. Specifically, there is research on the Johnsen-Rahbek effect with electrostatic adhesion, as well as the capstan effect and the use of tension for increased friction. This Capstan Clutch was the first design optimized for a 100Nm holding torque.
The shaft is designed to connect to a 300V power source, while the band, which attaches around the shaft, is connected to ground. When powered, the band grabs on to the shaft, acting as a clutch.
Includes:
-
A stainless-steel band, acting similarly to a spring, with band width, gap length, and depth measured using optimized values, that wraps around an aluminum shaft
-
Springs used to allow adjustment of the pretension, to help with initial connection between the band and shaft
-
Input and output mounting plates
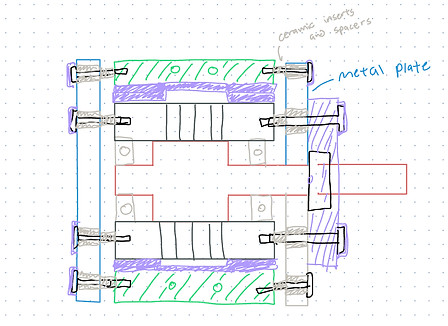
Initial design sketch - section view
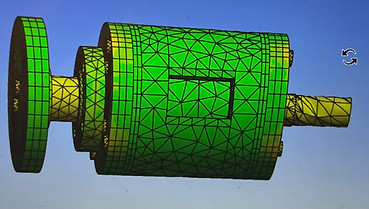
Deformation simulation results

Tools:
-
Fusion360
-
Ansys
Skills:
-
Design for Manufacturing
-
Design for Assembly
-
3D Printing
-
Finite Element Analysis
-
Material Selection
Capstan Clutch CAD section view
Contributions:
-
Designed many iterations of the Capstan clutch that were presented during weekly design reviews
-
Focused on efficient and compact insulation using 3d printed parts, ceramic inserts, and ceramic bearings to ensure safety for users
-
Ran simulations to ensure that the clutch was durable enough to withstand up to a 100Nm torque if made with aluminum
-
Called and worked with many different manufacturing companies to ensure manufacturing feasibility
-
specifically for the band, which includes precise cuts and measurements
-

CAD exploded view

-
Applied a PBI polymer layer and carbon tape to the shaft for help with adhesion
-
Assembled the Clutch and began initial testing with small applied torques
-
Adjusted the insulation and pretension for better results
-
Testing and adjustments are currently in progress to achieve 100Nm of holding torque
Final assembly reults