Berkshire Grey

Mechanical Engineering Co-op
July-December 2024
Berkshire Grey is a robotics company that uses AI to automize supply chain and fulfillment operations. During my 6 months as a co-op for this company, I worked on 2 different projects: RPSi (Robotic Package Sortation with identification) and RPU (Robotic Package Unloader). RPSi autonomously sorts and tracks large volumes of small sized packages. RPU automizes the long and tiring task of unloading delivery trucks with varying sizes, weights, and shapes of packages. Here are some of the projects that I worked on as a mechanical engineer on these projects!
Disclaimer: Some of the projects that I worked on at this company will have missing information or will not be included all together due to request of the company.
Linear Sort Wing Shuttle Bucket
RPSi
Context: The shuttle bucket is a bucket that moves along a linear rail and transfers packages to their assigned bags.
Task: Redesign the shuttle bucket to be easier to assemble and test the assembly on the machine.
Contributions:
-
Made final adjustments in CAD to make sure everything fit and is manufacturable
-
Created part and assembly drawings for the redesigned parts
-
Worked with manufacturers to get the parts made and ordered any additional components
-
Assembled the new Shuttle Bucket and took note of any assembly issues
-
Adjusted the CAD according to the discoveries made while assembling
Tools and skills:
-
SolidWorks
-
Part and assembly drawings



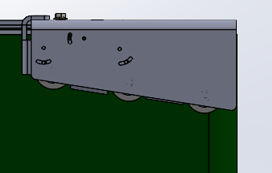
Linear Slide Testing for a Sweeper
RPSi
Context: A sweeper runs on a linear slide to push boxes into the shuttle bucket on the RPSi. The current linear slide being used is very expensive, so the team is looking to replace it with something cheaper.
Task: Test a new linear slide to determine its force and speed capabilities, test its different functionalities, and ultimately decided if it is worth using for the RPSi machine.
Contributions:
-
Set up the linear slide for testing
-
Adjusted the shelf that the motor is mounted to, and added a plastic flooring to simulate the machine
-
Added an 8020 frame to the sweeper to allow it to easily and consistently push boxes of different weights
-
Mounted a counter for life-cycle testing
-
-
Learned how to use the application to control the linear motor, and updated the instructional wiki
-
Tested varying speeds and weights with the motor while also adjusting the settings to optimize results
-
Worked with the vendors to resolve issues in the app
-
Created test plans for weight vs. speed, stalling, and life-cycle testing
Tools and skills:
-
Collaborating with vendors
-
Testing new systems



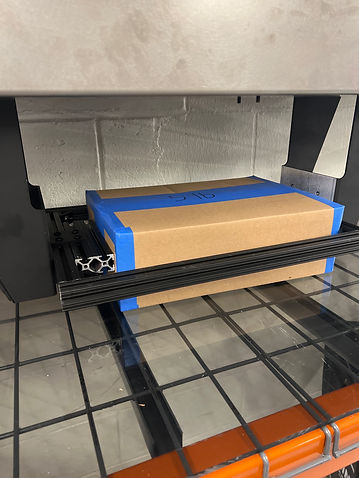
Conveyor Sensor Brackets
RPU
Context: Originally, the conveyors used lidar sensors to detect when boxes got stuck. The brackets for these were too flimsy and boxes often got stuck on it. Additionally, the lidar sensors were already very big, so most brackets got in the way when the conveyors were folded. Eventually, the lidar sensors were changes to 3, much smaller distance sensors.
Task: Redesign the lidar sensor brackets to be easily manufacturable, not get in the way of the machine when the conveyors are folded up, and be strong enough to withstand the impact of heavier boxes.
When we shifted to smaller distance sensors, my task was to created new brackets for the 3 sensors with given positional constraints.
Contributions:
-
Redesigned sheet metal lidar brackets to be easily manufacturable with limited mounting holes to the conveyor
-
Designed new sheet metal brackets for 3 differently positioned sensors
-
Tested the brackets on the machine and made changes based on any issues
-
Round 1 of testing: boxes got jammed along the sides, so rollers mounted at an angle were added to prevent this
-
Round 2 of testing: boxes got stuck on a corner, so the corner was cut flat
-
Round 3 of testing: a box got jammed, bending the thick stainless-steel brackets, so an additional bracket support was added
-
Tools and skills:
-
Sheet metal design
-
SolidWorks
-
Iterative design
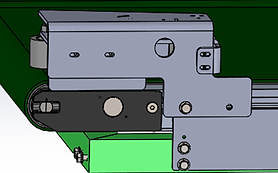


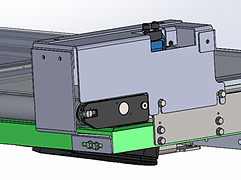





Original Lidar brackets
Lidar sensor bracket redesign
Distance sensor brackets original design
Distance sensor brackets redesign
Final distance sensor design
Distance sensor brackets support
Lagging bracket
RPU
Task: Redesign many different variations of a bracket that mounts to a system and lags to the floor, fits given size constraints, and can withstand 1000lb of force 27in above the bracket
Contributions:
-
Designed 5 different brackets using sheet metal, welding, and tubes that attach to a system and lag to the floor
-
Ran FEA on every bracket at 2-3 different orientations
-
Compared the deformation and stress results for each bracket

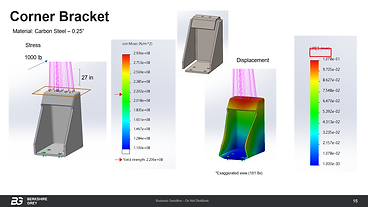
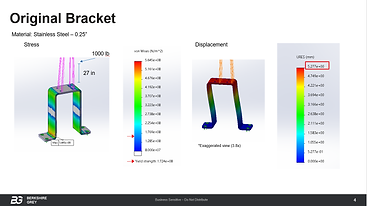
Final lagging bracket tube design
FEA of original design
FEA of sheet metal with welds design
Tools and skills:
-
Sheet metal design
-
Weld design
-
Tube design
-
FEA
-
SolidWorks
Conveyor Testing
RPU
Task: Do testing on a conveyor to compare speed vs. weight and determine when it stalls. Use this data to determine if the conveyor is fit to replace one that is currently being used.
Contributions:
-
Designed and built an 8020 frame to mount the conveyor at a 20-degree angle
-
Tested the motor with varying weights on it and recorded the changes in speed with the increase in weight
-
Increased the weight until the motor stalled and recorded the value
-
Concluded that the conveyor was not strong enough for the given application
Tools and skills:
-
8020 design
-
Testing


Miscellaneous
Tools and skills:
-
CNC and lathe machining
-
Sheet metal design
-
Creating and updating ECOs
-
DFM
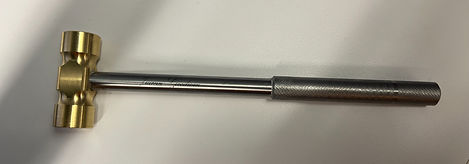
2 part hammer machined on the lathe





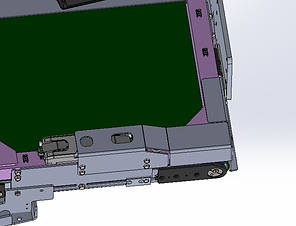




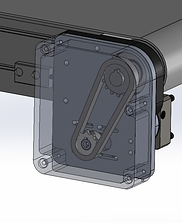

Conveyor chain cover
Conveyor wire cover
Conveyor MDR cover
Camera bracket
Conveyor gap fill
Sensor bracket
CNC machined brackets